光栅尺与对刀仪工件厚度控制法
在纺织机械领域,有必要使用表面质量非常光滑的陶瓷零件作为导丝。在传统陶瓷毛坯磨削减薄过程中,需要人工去除工件并测量其厚度。在达到所需的尺寸公差的过程中,每件工件往往需要2~3次重复测量,且效率较低。
为了提高加工效率,有必要解决加工尺寸的自动控制问题。目前有多种厚度检测方法,如电磁检测、声发射传感器和激光测距仪。但上述方法存在只能检测金属零件或抗冲击、振动能力差、检测精度不高、设备成本高等缺点。目前使用这种磨床很困难。因此,寻找一种相对简单、实用、能满足精度要求的自动检测与控制方法具有十分重要的意义。
一、工件尺寸测量的常用方法
陶瓷工件的尺寸规格较多,各种工件所要求的精度等级也较高,本文以图1所示工件为例进行说明,图中a为磨削过程中所需减薄尺寸。测量尺寸的方法可以分为直接测量法和间接测量法。
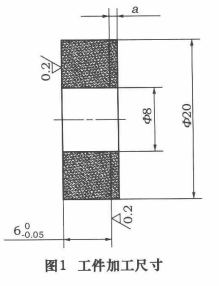
1.1直接测量法
(1)手工离线测量手工取下工件并测量工件尺寸,在批量生产过程中,反复的加工与检测,工人劳动强度大。
(2)磨床在线主动测量装置测量
该装置只能测量工件外圆,获得工件的直径尺寸数据,无法获得工件厚度尺寸,无法解决工件厚度尺寸在线检测与实时显示的问题。
1.2间接测量法
通过检测元件检测其与工件被加工面之间的相对距离也可以间接获得工件的厚度尺寸。可以实现间接测量的方法主要包括以下几种:
(1)自动测头
数控机床在工件尺寸检测中常用到自动测头。该类型测头的优点是检测精度高,但缺点是需要在停机状态下使用。该类型测头在批量自动减薄加工过程中并不适用。
(2)激光测距传感器
激光测距传感器用于产品厚度检测、相对距离检测等场合,其精度可以达到7 μm、20 μm、40μm等。其优点有:测量精度较高、量程大、体积小、安装调试方便、在线式连续测量等。
(3)其他方法
除以上的常用测距方法外,还有超声波检测法、磁性测厚法、涡流测厚法、电解测厚法等。以上各种常见方法中7μm级激光测距传感器可以达到检测要求的精度。但该检测元件抗振性较差,并且在不停机状态下在线检测对机床机座的刚性要求非常高,如果中间停机检测又降低了加工效率,而且切削液的存在也对该方法的检测精度产生影响,不适合用于该型专用磨床的场合。其他方法由于不耐振或者精度较低、价格昂贵等原因也不适于在本磨床场合应用。
二、光栅尺与对刀仪组合用检测装置
在对比各种检测方法的精度、可靠性、性价比的基础上,本方案提出采用光栅尺与对刀仪组合使用的检测装置,通过程序可以自动控制实现工件厚度尺寸的精确控制。
2.1光栅尺与对刀仪组合系统的介绍系统组成如图4、图5所示,检测部分主要由光栅尺与对刀仪组成,通过伺服电动机驱动滚珠丝杆带动工作台及砂轮进行往复运动,光栅尺是通过工作台与砂轮相连的,通过光栅尺的数据输出可以在显示屏上实时反映砂轮进给过程中工件厚度的变化,由系统依据程序算法控制砂轮的自动进给距离即可控制工件减薄后所剩尺寸。
系统控制电磁阀的动作对摆动气缸动作进行控制,由摆动气缸带动对刀仪进行摆动过程,每个加工区段按照定额的30个工件加工完成后,摆动气缸带动对刀仪旋转至砂轮的进给通道上,进行一次对刀,对刀完成后,摆动气缸带动对刀仪离开砂轮进给通道,通过对刀过程对上个加工区段的砂轮磨损的累积误差进行清零,确保新的区段的加工过程中工件尺寸的精度。
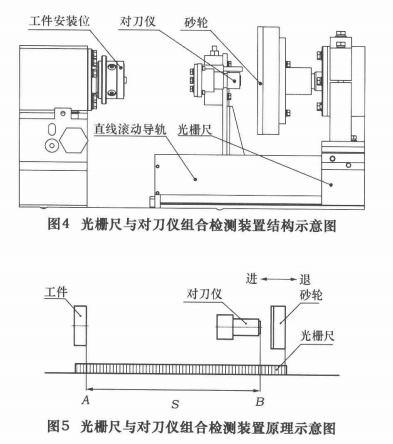
由于工件加工的精度要求较高,因此对摆动气缸的安装精度与对刀仪本身的对刀精度都提出了较高的要求。经计算选用安装精度在+0.01 mm的MSQB-10型摆动气缸,选用重复定位精度在2 μm的TTC- 100型对刀仪。综合以上的因素,可以满足定位精度要求。且通过调试过程将实际测得的摆动气缸与对刀仪的安装偏差量进行消除,可以达到更高的定位精度。
2.2该测量装置的关键原理
光栅尺在其有效的行程上可以精确的定位,其定位精度可以达到±3μm,分辨率可以达到1 μm甚至0.5 μm,可以用来实时准确地反映砂轮在行程上的位置变化。图5中A为工件达到所要求的工件标准尺寸时砂轮的进给停止位,B处为对刀仪提供的砂轮进给起点位,A、B之间的距离S即为砂轮标准进给行程。如果不考虑砂轮的磨损,那么起点与工件加工目标位置之间的行程s是固定的,理论上系统只要按照设计的行程S控制砂轮进给距离即可精确控制工件的厚度。但实际上砂轮磨损并不能忽略,如果不考虑砂轮磨损的补偿,加工一定数量后由于砂轮磨损积累会使工件尺寸逐渐加大,最终工件尺寸超出允许公差值就会导致废品的出现。
通过批量加工测量得到的数据,发现实际加工过程中每个工件砂轮磨损消耗量△非常小,在加工过程中设置一个经验平均值0对砂轮磨损量予以补偿,那么就可以消除砂轮磨损影响,可以较高精度地控制工件尺寸。砂轮进给距离算法程序为:
加工第一件:S1=S
加工第二件:S2=S+△
加工第n件:Sn=S+(n-1)△ (1≤n≤30)
加工第30件: S30 =S+29△
在控制系统中通过光栅尺的数据反馈,通过控制砂轮进给距离控制工件的厚度,那么依据上面的算法,对经验平均值△来说其越接近实际磨损消耗值,机床加工获得的工件的精度越高。在经验值△一定的情况下,实际加工过程中有几个因素会影响到砂轮实际消耗量A,主要影响因素如下:
工件规格不同加工表面面积不同,如φ20mm与φ32 mm对砂轮消耗量不同;
②砂轮磨削层材料致密性不同导致硬度不均匀;
③工件坯料需减薄厚度a值不一致。
以上3个因素都会导致每个工件砂轮磨损消耗量△不相同,因此较准确地测量每个工件的砂轮磨损消耗量△成为一个重要因素。通过对以上3个因素进行测定后,建立每种规格工件对应的砂轮磨损消耗量经验值A的数据库,并将该数据保存在控制系统中,每一批工件加工开始前依据实际情况在显示屏操作面板上进行设置即可调用经验值△。
在上述加工中砂轮磨损补偿算法得到明确后,需要解决砂轮磨损累积偏差清零的问题,加工完一个区段30件后,毕竟经验值与实际值是有偏差的,其经验累积补偿值与实际累积砂轮磨损量的偏差如何消除,只有将这个累积误差消除,才能保证下一个30件加工批次的精度。为了消除累积误差,我们利用对刀仪的定点信号输出的特点,利用程序控制在每个30件加工段的开始前进行一次对刀,找到砂轮的准确的起点,对砂轮磨损消耗量累积偏差进行清零,以AB之间的距离作为砂轮进给标准行程S,加工中再次按照砂轮磨损补偿算法控制砂轮进给距离,即可精确控制每个加工段各个工件的厚度尺寸。
三、结语
通过光栅尺和对刀仪的结合使用,解决了精确定位、砂轮磨损补偿、累计误差清除等几个重要问题,实现了端面磨床的工件减薄过程,成本低,可靠性高,工件厚度自动控制,与传统的直接检测激光测距仪相比,具有明显的抗振动、抗切削液干扰、成本低等优点,声发射传感器等方法。可在同类磨床设备或自动加工线上推广应用。它可以提高设备或系统的自动化程度,提高处理效率。
|