多刀位数控机床对刀仪设计
在使用四刀位数控车床加工零件时,通常用垫片垫车削刀具,以保证车削刀尖的车削中心和数控车床主轴的高度,以保证加工精度。部分。但是,由于工具杆的厚度不同以及每个车刀的刀片安装高度不同,为了确保车刀尖端的高度与主轴的旋转轴相等,必须选择合适的垫片厚度以垫住车刀,很难找到合适的垫片厚度,这不可避免地导致车刀尖端高度与主轴旋转轴线不相等,从而导致刀具安装错误。分析了刀具加载高度误差引起的加工误差,得出结论:刀具加载高度误差不仅影响零件的尺寸精度,而且影响零件的形状精度,并提出解决工具加载高度误差对零件加工质量影响的措施。由车削刀尖高度和主轴旋转中心高度不相等引起的刀具加载高度误差对零件的加工精度影响很小,很容易忽略。例如,常用的试切法和ATC法更注重工具在横向和纵向上的误差的校正,而较少关注工具装载的高度误差。但是刀具装载的高度误差对精密加工有很大的影响。开发一种精确的对刀装置,以减少刀具装载的高度误差,提高加工精度,并确保零件的加工质量,这一点非常重要。本文在不改变数控车床结构的基础上,开发了一种精密的对刀装置,该装置以螺杆斜滑块机构为刀具高度调节机构。该装置可以保证工具安装的准确性,安装简便,安全可靠。
一、精准对刀装置的设计
1.1设计要求
要实现数控车床精准对刀,保证零件的加工质量,提高工作效率,设计出的精准对刀装置需满足以下要求:
(1)车刀刀尖高度调整方便、快捷、精准;
(2)车刀夹紧安全、可靠,在切削力作用下不发生位置偏移;
(3)精准对刀装置安装方便、可靠。
1.2结构设计
为满足精准对刀装置的设计要求,作者设计出了方便快捷的精准对刀装置。其结构示意图如图1所示。
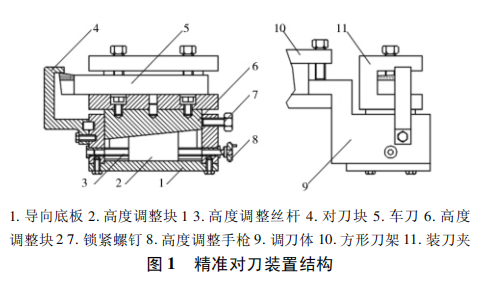
此装置的装刀夹11通过内六角螺栓与高度调整块2紧固,高度调整块1与高度调整块2以斜面接触,通过高度调整手轮8带动与高度调整块1相旋合的高度调整丝杆3转动,可以使高度调整块1沿导向底板1的导轨左右移动,从而推动高度调整块2沿调刀体9的导轨.上下移动,实现装刀夹的高度调整。
为保证对刀的精准、快捷、方便,在调刀体9上安装一个方便拆卸的对刀块4,对刀块4的对刀面在精准对刀装置安装在数控车床四刀位刀架上时应与数控车床的主轴回转轴线等高,当调整车刀刀尖到达对刀块4的对刀面时即可认定刀尖已与数控车床回转轴线等高,并用锁紧螺钉将高度调整块1锁紧。此项刀尖高度调整工作可在精准对刀装置安装在数控车床四刀位刀架前完成,不占用机床加工零件时间。
1.3具体操作说明
(1)将车刀5安装在装刀夹11 上,用紧定螺栓紧固,转动高度调整手轮8使装刀夹下降,并将装刀夹往下压实,保证高度调整块2和高度调整块1相互接触;.
(2)将对刀块4安装在调刀体9.上,紧 固;
(3)转动高度调整手轮8使车刀刀尖缓慢向上移动,直至车刀刀尖与对刀块4的对刀面接触,拧紧锁紧螺钉7对刀尖高度锁定;
(4)拆除安装在调整块9.上的对刀块4;
(5)将精准对刀装置安装在数控车床四刀位刀架上,并用紧固螺栓紧固。
二、精准对刀装置关键零件加工工艺要点
2.1对刀块的对刀面加工工艺要点
如前所述,调整数控车刀刀尖高度时,只要将刀尖调整到与对刀面相接触就可认定其与数控车床的主轴回转轴线等高,这就要求精准对刀装置在数控车床四刀位刀架.上安装时,对刀块的对刀面需与数控车床的主轴回转中心等高。
机床生产厂家在数控车床出厂前已经保证了其尾座套筒中心线与主轴回转轴线等高,则安装在尾座套筒中固定顶针的顶尖就处于主轴回转轴线上而与主轴回转轴线等高,只要保证了精准对刀装置的对刀面与固定顶针的顶尖等高,就可保证数控车刀刀尖与对刀面接触时刀尖与数控车床回转轴线等高。因此,为满足对刀块的安装要求,可以依据“自为基准”原则来完成对刀块的对刀面加工,其加工工艺要点是:利用安装于数控车床尾座上固定顶针的顶尖对安装在数控车床四刀位刀架上的精准对刀装置对刀块进行划线,并以此线为基准完成对刀块的对刀面加工。
2.2高度调整块螺纹孔和调刀体丝杆支承孔的加工工艺要点
在对刀过程中,通过高度调整块螺纹孔与高度调整丝杆的相互旋合,可以调整数控车刀的高度来实现刀尖与数控车床的主轴回转轴线等高。为保证数控车刀高度调整灵活、快捷,高度调整丝杠在车削加工过程中不应该承受切削力的作用而发生弯曲变形,切削力可以通过高度调整块由导向底板承担。为满足高度调整丝杠转动灵活实现数控车刀的高度调整,需要保证高度调整块螺纹孔和调刀体两高度调整丝杆支承孔同轴,并且要提高导向底板与调刀体、高度调整块的装配精度。因此,在高度调整块螺纹孔的加工工艺上,可以采用“合件加工”的方式来完成高度调整块螺纹孔、调刀体两高度调整丝杆支承孔的定位加工。如图2所示,在高度调整块螺纹孔以及调刀体两丝杆支承孔加工之前,将调刀体、导向底板和高度调整块按图示方法进行紧固,然后利用加工中心对调刀体两丝杆支承孔、高度调整块螺纹孔一次性钻孔,最后再对各孔按各自技术要求进行加工。
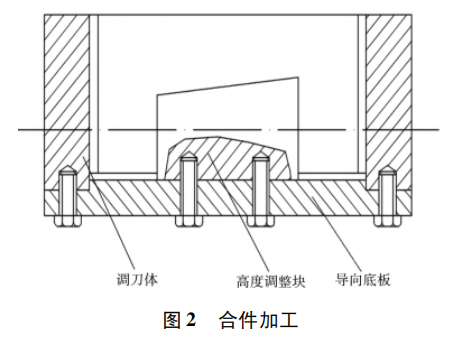
通过试制,采用此加工工艺既保证了各孔的同轴度,又保证了装配精度,高度调整丝杆转动灵活,达到了设计的技术要求。
三、精准对刀装置的受力分析
在车削过程中,如果数控车削工具要从毛坯上切下切屑,则必须对毛坯施加力。在该力的作用下,切屑材料将发生弹性变形,塑性变形,甚至断裂,这将从母材上剥离。根据力和反作用力的原理,在车削过程中,切屑材料还使数控车削刀具具有抗后切削力,即切削力F。如图3所示,切削力F可分为分为三个相互垂直的分量,一个是沿进给方向的进给分量f,一个是垂直于工作平面的反作用力FP,另一个是沿主运动方向的主切削力FC。真力Fp和进给力F的合力为Fz,推力Fz作用在切削层的平面上并垂直于主切削刃。
如图3所示,在车削过程中,使用强大的力Fp和进给力Ff将NC车刀推向NC车床的X轴和Z轴的正方向,以便NC车床工具离毛坯很远。在精密工具设置装置中,有7个锁紧螺钉7以防止NC车刀沿X轴正方向移动,高度调节块防止NC车刀沿Z轴正方向移动。在锁紧螺钉7和高度调节块2的共同作用下,可以确保数控车刀不会沿x轴和z轴的正方向移动,并且可以确保数控车刀的位置CNC车床在X轴方向和Z轴方向上的稳定性稳定,这对于提高零件的加工质量尤为重要。主切削力FC主要作用在NC车刀的垂直方向上。按下数控车刀时,由于刀具装置的精确高度调节块2和导向基板的共同作用,可以抵抗主切削力FC,从而避免了数控车刀的下移。
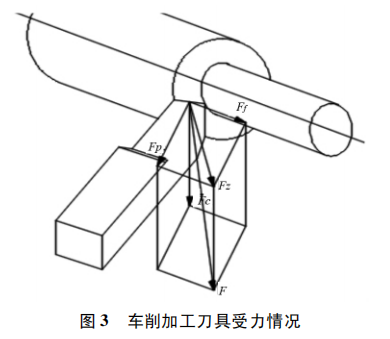
通过以上分析可知:此精准对刀装置在车削加工过程中稳定可靠,具有良好的刚度,能保证零件的加工精度。
四、精准对刀装置的加工精度测试
为验证研制的精准对刀装置对零件加工精度的影响,分别利用传统对刀方式和精准对刀装置对刀方式,在某厂生产的CKA6140型数控车床上对如图4所示的测试样件进行车削,采用同- -加工程序加工,加工材料为40Cr。加工完成后,经测量,得出两种对刀方式的加工质量如表1所示。
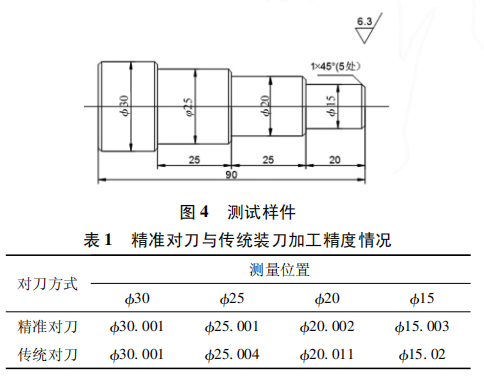
从测试结果对比可以看出:
(1)对刀高度误差是引起精密零件加工误差的主要因素;
(2)随着零件加工直径的逐步变小,由于对刀高度误差引起的零件加工误差越来越明显;
(3)采用精准对刀装置可以减少对刀高度误差,提高零件加工精度;
(4) 精密小零件的加工,采用精准对刀装置对刀车削,加工精度提高较为明显。因此,本精准对刀装置可以提高车削加工的零件加工精度,达到预期的目标。
五、结论
为了解决数控车床对刀精度低造成的加工误差问题,本文研究了精密对刀装置的设计方案,讨论了该装置关键零件的加工过程要点,并对应力进行了分析。该装置的设计与制造,是一种四刀位数控车床的精
确对刀装置,可以实现数控车床刀具的精确对刀,具有以下创新和研究意义:
(1)使用该装置,无需任何垫片就可达到刀尖高度和数控车床主轴轴线,从而提高了数控车床工具的安装速度和精度;
(2)使用该装置调整刀具,可以节省数控车床的闲置时间,提高加工效率;
(3)由于刀具磨损,传统的四位置刀架对刀具的精度影响很大。该装置可实现精确的工具对准,而不受工具规格,型号,厚度和工具磨损程度的影响;
(4)设计的精密对刀装置,结构简单,易于组装,对刀操作方便,避免了因拆卸而造成的工具损坏,足够的刚性,稳定性好,保证了零件的加工精度。
(5)每个精密对刀装置仅安装一个CNC车刀,可根据加工需要为该装置安装不同的车刀,适应性强,在加工时不改变原有CNC车床的结构工具已安装;
(6)在精密小零件的车削过程中,装置的对刀可以提高零件的加工精度。
|