数控雕刻对刀仪设计
数控机床可在圆柱面、锥面、平面上雕刻各种文字、曲线、图案。单台数控雕刻机成本高,加工效率不高。多位置夹具可以大大提高雕刻效率,但多位置夹具最大的问题是由于加工和制造的原因,每个工件的尺寸和公差不能完全一致。
例如,在圆柱体表面雕刻刻度和文字,刻线深度一般为0.02--0.05mm。如果有一个错误在工件的直径(一般的误差是0.01--0.05毫米),如果有圆柱度误差,线的深度的中心是深,一边远离中心可能是浅,不能满足处理要求。同样,平面和锥面雕刻也存在上述问题。为了解决这一问题,特别是对于仪器仪表上的刻度等高精度雕刻,必须使用专用的雕刻工具对刀装置。
一、对刀仪的机械结构与工作原理
如图,雕刻机机座机体连同工作台、夹具、工件都为良导体,接到5V电源的地上,雕刻头固定在机体上时中间采用一层特殊绝缘材料在电路上与机体隔开接5V电源正极。数控系统发出对刀指令后对刀仪向Z轴进给电机发出向下步进一个脉冲(步距为0.001mm)的指令,然后检测雕刻头电信号是否为低电平,如为低电平表示雕刻头接触到工件,如为高电平表示雕刻头还未接触到工件,继续发出进刀指令。对刀精度不大于0.002mm。
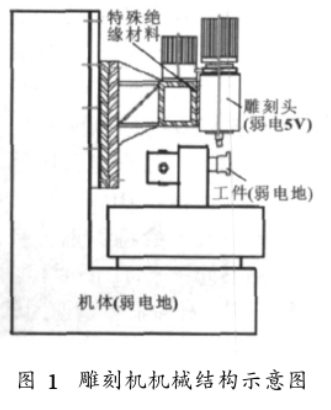
多工位数控雕刻机对刀仪采用多个独立控制系统分别控制多个雕刻头在每次雕刻进刀前自动对刀检测(配备专用数控系统,在进刀前由每个对刀控制系统独立工作,对刀完成后由数控系统统一发送运动指令)。对刀采用电接触检测,雕刻头和工件分别为5V电源正负极,接触后检测到相应电信号立即停止对刀。由于刀具处于高速旋转状态,要实现电信号可靠检测,需在雕刻头外固定件与高速旋转主轴之间采用石墨碳刷压紧接触,保证电平信号可靠和连续性。该方法检测灵敏度高误差小于0. 002mm,在实际使用中扎刀概率小于0. 0001%。
二、对刀仪电路设计
多头对刀仪采用多个独立单片机控制系统,完成功能主要有如下几个方面:
(1)等待数控系统发出对刀指令,接受到对刀指令后开始对刀动作。对刀动作完成后返馈对刀完成信号给数控系统。
(2)数控系统随时可以解除对刀状态。
(3) 不对刀时接收数控系统发出Z轴脉冲指令,再将该脉冲指令发送给本单片机系统控制的电机。实现Z脉冲的分配。
三、可靠性保证措施
对刀仪的引入可以解决上述问题,但也带来了严重的问题。如果刀具设置信号有问题,将进行刀具绑定。刀具继续向下运动,碰到工件表面仍继续向下运动,会造成严重的刀碰事故,必须避免,否则雕刻机无法正常运行。为避免粘刀现象,采取以下可靠性保证措施:
(1)雕刻头采用特殊设计结构。整个雕刻头作为电极,但在雕刻头结构图中可以看到雕刻头体与中间高速转轴在做高速旋转相对运动。可以说,这两个导体之间的接触不是100%可靠的,所以在检测刀尖电信号时会出现错误。实验结果表明,这种结构能使切削率提高1% ~ 5%,严重影响性能。为了提高检测的可靠性,在雕刻头的上端增加了一个紧凑的石墨碳刷装置。石墨碳刷通过弹簧压力靠近高速主轴。使用此结构后,实际绑定率不超过0.0001%。目前客户使用中没有约束性报告。
(2)高速主轴电机采用直流无刷电机。一方面,直流无刷电机的转速可达10000 R / min,与相同转速的交流相比,目前的主轴价格便宜很多。此外,与普通直流电动机相比,运行稳定可靠,无电磁干扰,也大大降低了扎刀的概率。
四、结语
多工位数控雕刻机已成功应用于全自动数控五轴雕刻机,并取得了良好的效果。生产效率提高了6~7倍。该技术可应用于数控雕刻机的精密雕刻,如各种仪器仪表的校准、步枪瞄准镜的校准等,也可广泛应用于数控铣床、加工中心等多工位加工系统中。对刀仪精细化加工
|