数控铣床和加工中心对刀
1、机外对刀仪
机床外的对刀装置可进行X、Y、Z方向的对刀。
如图所示,主要测量刀具的长度、直径、形状和角度,并准确记录预执行刀具的主要参数。如果使用的工具损坏,需要更新的主要参数值的新工具可以测量工具设置仪器,掌握偏离原来的工具,然后正常的加工可以保证通过修改工具补偿价值。
对刀仪的测量方法如下:
(1)使用前,用标准对刀轴进行校准。每个对刀仪器都配备一个标准的对刀心轴。应防止因外力而腐蚀或变形。z轴和x轴的尺寸在每次使用前都要进行校准。
(2)当使用标准对刀心轴从参考点移动到工件零点时,读取X、y。z坐标在机床坐标系下,将X、Y值输入工件坐标系g54参数,将z值叠加到芯轴长度后输入到g54。
(3)对刀仪上其他刀具测量的刀具长度值补偿到相应的刀具长度补偿数。
在静态测量的刀具尺寸和实际加工的尺寸之间存在差异。静测的刀具尺寸应大于加工后实际孔的尺寸,对刀时应考虑校正,对刀应根据操作者经验预选,一般大0.01 ~ 0.05mm。
二、刀具X、Y向对刀方法
X、Y向对刀的目的是在零件装到数控铣床或加工中心工作台上以后,测量出工件坐标系与机床坐标系的偏差值,用G54~G59对该值进行坐标系偏置。
(一)对刀点为圆柱孔(或圆柱面) 的中心点.
(1)采用杠杆百分表(或千分尺)对刀,如图4 -45所示。其操作步骤如下:
①用磁力表座将杠杆百分表吸在机床主轴端面上,并利用手动输人MO3由低速正转。
②手动操作使旋转的表头依X、Y .Z的顺序逐渐靠近孔壁(或圆柱面)。
③移动Z轴,使表头压住被测表面,指针转动约0.1mm。
④逐步降低手动脉冲发生器的X.Y移动量,使表头旋转一周后 ,其指针的跳动量在允许的对刀误差内,如0.02mm,此时可认为主轴的旋转中心与被测孔中心重合。
⑤记下此时机床坐标系中的X、Y坐标值。此X、Y坐标值即为G54指令建立工件坐标系时的偏置值。若用G92建立工件坐标系,保持X、Y坐标不变,刀具沿Z轴移动到某一位置,则指令形式为:“G92 X0 Y0;"”。
这种操作方法比较麻烦,效率较低,但对刀精度较高,对被测孔的精度要求也较高,最好是经过铰或镗加工的孔,仅粗加工后的孔不宜采用。
(2)采用寻边器对刀。光电式寻边器一般由柄部和触头组成,常应用在加工中心上。触头和柄部之间有一个固定的电位差,触头装在机床主轴上时,工作台上的工件(金属材料)与触头电位相同,当触头与工件表面接触时就形成回路电流,使内部电路产生光电信号。如图所示。其操作步骤如下:
①把寻边器装在主轴上。
②依X.Y.Z的顺序手动操作将寻边器测头靠近被测孔,使其大致位于被测孔的中心上方。
③将测头下降至球心超过被测孔上表面的位置。
④沿X(或Y)方向缓慢移动测头直到测头接触到孔壁,指示灯亮,然后反向移动,使指示灯灭。
⑤降低移动量,移动测头直至指示灯亮。
⑥逐级降低移动量(0. lmm ~0.01 mm ~0.001 mm),重复上面④、⑤的两项操作,最后使指示灯亮。
⑦把机床相对坐标X(或Y)置零,用最大移动量将测头向另一边孔壁移动,指示灯亮,然后反向移动,使指示灯灭。
⑧重复操作第④~⑥项的操作。
⑨记下此时机床相对坐标的X(或Y)值。
10.将测头向孔中心方向移动到前- -步骤记下的X(或Y)坐标的1/2处,即得被测孔中心的X(或Y)坐标。
11.沿Y(或X)方向,重复以上操作,可得被测孔中心的Y(或X)坐标。这种方法操作简便、直观,对刀精度高,应用广泛,但被测孔应有较高的精度。
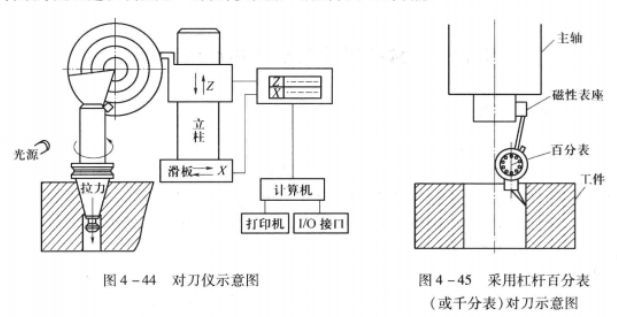
(二)对刀点为两相互垂直直线的交点
1.采用刀具试切对刀
如果刀具精度要求不高,为方便操作,可以采用加工时所使用的刀具进行试切对刀。其操作步骤如下:
①将所用铣刀装在主轴上,并使主轴中速旋转。
②手动移动铣刀沿X(或Y)方向靠近被测边,直到铣刀周刃轻微接触到工件表面,听到刀刃与工件的摩擦声(但没有切屑)。
③保持X、Y坐标不变,将铣刀沿+ 2向退离工件。
④将机床相对坐标X(或Y)置零,并沿X(或Y)向移动刀具半径的距离。
⑤此时机床坐标系下的X(或Y)值输人系统偏置寄存器中,该值就是被测边的X(或Y)坐标。
⑥重复以上操作,可得被测边的Y(或X)坐标。
这种方法比较简单,但对刀仪对刀精度不够高,会在工件表面留下痕迹。为了避免损坏工件表面,在刀具和工件之间插入塞尺来制造刀具。在这种情况下,应减去测隙规的厚度,但不应旋转主轴。同样,标准芯轴和块规也可用于设置刀具。
|