简单的开环控制数控车床,由于不具备位置检测功能,操作者只能通过卡尺或通过刻度盘读数来测量,大致确定刀具在机床坐标系中的初始位置,即实现所谓的零位操作,从而得到刀具的坐标值机床坐标系中的刀位点。其次,对于安装在多个刀具上的简单数控车削刀架,每个刀具点(车削刀尖)在机床坐标系中的位置不同,刀具与标准刀具点之间存在相对位置偏差,即所谓的刀具补位。为了获得加工程序所需的刀具补充数据,刀架上的每一个刀具都需要以类似于零操作的方式操作,这增加了许多人为因素,降低了加工精度和生产率(特别是在形状更复杂、刀具使用更频繁的情况下)。目前,国内的数控车床刀具是利用机床数控系统的实时坐标显示功能来实现刀具X轴(工件直径)和Z轴(工件长度)方向的刀具刀具,但不能自动计算刀具的补刀量值。对刀仪能自动获取刀尖位置,计算出刀具补刀量,节省了对刀时间。刀臂设计用于回转,重复定位精度高,有效利用空间,具有一定的创新性。
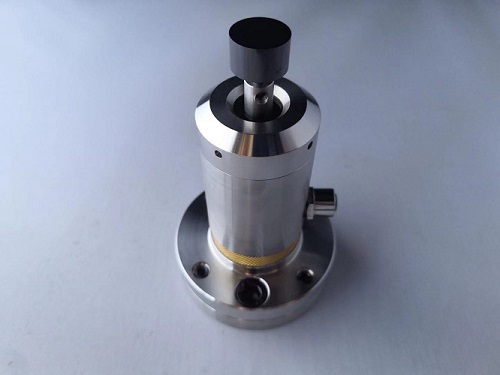
对刀仪的原理分析
当刀具用于工具仪器时,首先要知道标准刀具和工件的相对坐标。一般来说,标准刀具是为刀具仪器自动设置的。当刀具用于刀具时,首先将标准刀具用于刀具,然后设置其他刀具相对于标准刀具的刀具位置偏差,即刀具补码值。刀具仪表装有传感器,刀具最初归零,即回到机床原点,使刀具有一个统一的参考点;刀具移动后,系统记录实时坐标,通过程序进行采集和计算。刀具在手动模式下,控制刀具快速向传感器方向移动,当切削刀具接近传感器弹性块时,缓慢进给光接触传感器,传感器的机械精度很高,并能补偿刀具过冲,精加工表面,防止传感器损坏,当触发时,传感器电路内部产生触发信号,经过识别加工刀控制装置,把指令传到原机床数控系统的传动单元,控制刀具停止运动,这个过程很短,而且刀具是慢进给的,所以停止机床的位置,可视为触发瞬时切削刀具的位置,此时按下按钮记录刀具位置并计算。这样,在传感器被触发之前执行另一方向的进给,并且可以获得该方向上刀具的位置坐标。当获得X和Z方向的位置时,刀架可以自动返回起点并旋转到下一个刀具位置以继续刀具对齐,直到所有刀具对齐为止。
刀具仪传感器的设计
1.传感器倾角设计
设计中考虑的车刀类型主要有:圆柱车刀、端面车刀、螺纹车刀和内孔车刀。车刀的形状和角度不同。在x方向,当平面传感器信号平行于z轴时,可以触发所有刀尖。但Z方向不同,随着平面传感器信号平行于X轴,一些车刀(如螺纹车刀)第一次接触的不是刀刃的点,所以要考虑使这一侧成为斜面。现在,传感器的弹性接触面倾角为22°,可应用于主偏角22°以上的圆柱车刀、螺纹车刀和内孔车刀的端面。
2.结构设计
对刀仪的精度取决于传感器的精度,传感器由刀具直接触发产生触发信号,因此传感器的选择非常重要。本设计中的传感器选用电触发式传感器,当刀具与传感器接触并前进到设定的位移时,传感器将被触发,产生一个信号,对数控系统进行相应的数据处理后即可接收。
对刀仪主体结构:
主体结构由四个触发传感器组成。每个触发装置由弹性块、固定块、绝缘体、弹簧和导电装置组成。4个触发装置,2个为一组,上部为两个内孔车刀,下部为两个外圆车刀,端面车刀,螺纹车刀。其中1、3号传感器记录X方向坐标,2、4号传感器记录Z方向坐标。传感器(2号和4号)弹性块表面的Z角为22°。传感器弹性块表面要求较高的平面度和位置精度。当弹性块受到压力时,它会向内移动。当移动到一定距离时,它将与绝缘体上的导电块接触,从而闭合电路,使系统获得触发信号。同时,将绝缘块背面的弹簧固定在导电装置上也能起到一定的缓冲作用,从而保护导电块上的接触,使其不会因冲击而变形,从而保证了对刀仪的精度。
|