在用数控机床制造产品零件的过程中,影响零件质量的因素有很多,如数控机床的精度、工件材料、工件热处理、加工工艺、冷却剂、刀具等诸多因素。其中,刀具参数的准确设置很少受到人们的关注和重视。在这里,我们将重点介绍数控机床刀具精确整定方法的特点和发展趋势。
数控机床常用的对刀方法和对刀仪器
在以刀具为目的的数控加工过程中,数控程序的路径就是刀尖在主轴上的运动路径。从开始到结束,刀具位置的移动路径需要在机床坐标系中精确控制,因为机床坐标系是机床唯一的参考。程序员在编程时不可能知道各种工具规范的具体尺寸。为了简化编程,在编程时必须使用统一的基准。然后,在使用刀具进行加工时,将刀具的精确长度和半径尺寸相对于基准进行偏移,从而得到刀尖的准确位置。因此,刀具设定的目的是确定刀具的长度和半径,从而确定加工过程中刀具尖端在工件坐标系中的准确位置。
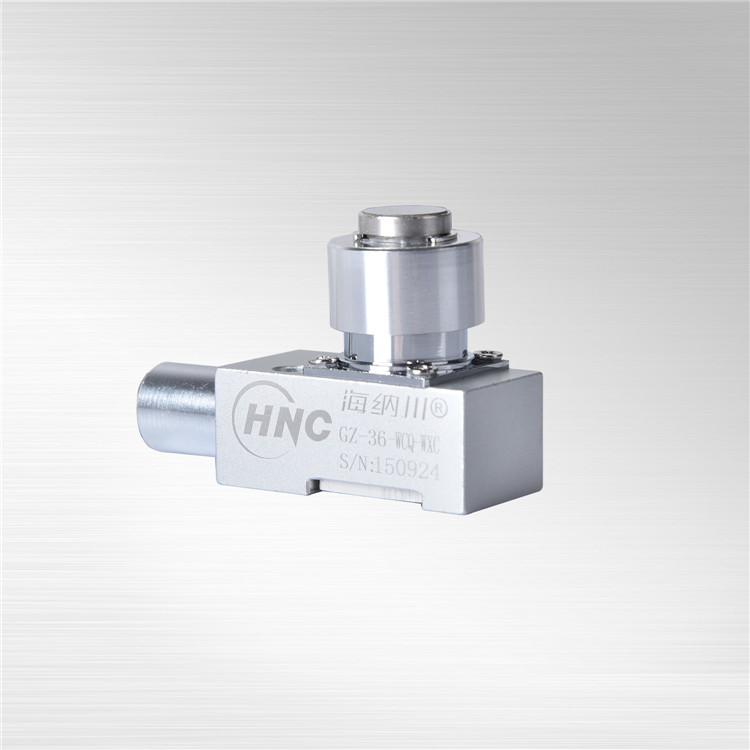
常用工具设置方法
刀具预置器是一种能够预先调整和测量刀尖长度和直径的测量仪器。如果仪器与数控机床形成DNC网络,则还可以远程将刀具长度和直径数据输入加工中心NC中的刀具参数。该方法的优点是刀具在机床外部预先标定,安装时即可使用,大大节省了辅助时间。然而,主要缺点是测量结果是静态值。在实际加工过程中,刀具磨损或损坏状态无法实时更新,机床热变形引起的刀具膨胀无法实时测量。
试切法定刀
试刀设定是在工件正式加工前,由操作者以手动方式操作机床。操作者根据眼睛和耳朵的判断来确定当前刀尖的位置,然后进行形式化处理。这种方法的优点是不需要在工具和设备上进行额外的投资,而且很经济。主要缺点是效率低,对操作人员的技术水平要求高,容易出现人为失误。在实际生产中,有许多派生的试切方法,如块法、着色法等。
机内对刀
这种机床对刀方式是利用机床工作台上设置的测量装置(对刀仪),对刀库中的刀具按预先设定的程序进行测量,然后与参考位置或标准刀具进行比较,得到刀具的长度或直径,并自动更新到相应的数控刀具参数表。同时,通过刀具检测还可以实现刀具磨损、损坏或正确安装型号的识别。
机内对刀仪一般由传感器、信号接口以及对刀宏程序软件组成。
根据传感器的工作方式,机刀仪可分为接触式刀仪和激光刀仪两大类。接触式刀表的重复测量精度为1米,根据刀表信号传输方式的不同,可进一步分为以下几类:电缆刀表;红外刀表;无线电刀表。
电缆式对刀仪:由于不需要刀具信号转换部件,且具有最佳的单一成本性能,所以在工作中最为常见,但其缺点是缆绳牵引,限制了刀具的应用场合,大多适用于中小型三轴铣床/加工中心。
红外线式对刀仪:信号传输范围一般在6米以内,其优点是采用了编码HDR(高速数据传输)红外技术,避免了电缆牵引带来的不便和潜在的安全威胁,刀子可以随时从工作台上取下,不占用处理空间,并可用于多台机床共用一台刀具仪表,从而降低整体成本。其缺点是在使用小型处理中心时,成本效益不高。根据其特点,该类工具主要用于中型机床和大型数控立车。
射电式刀具:射电信号传输距离一般在10米以上。其优点是无线信号传输范围大,不易受环境影响,刀后可随时从工作台上取下,不占用加工空间,并可多台机床共用一台刀具,从而降低整体成本。这种类型的刀具对用于大型/重型机床。
激光对刀仪:如hexagon的LTS35.60,是基于当激光束被旋转工具遮蔽时,使用聚焦激光束作为触发介质来产生触发信号的原理。而接触刀有本质不同的激光装置,对刀采用非接触式测量,刀在没有接触力的情况下,可以作为极其微小的工具进行测量,不必担心由于接触力而造成的微小的工具破损,如LTS35.60可测量工具直径可小至0.008mm(如钻头、丝锥或微铣刀等),其重复测量精度为0.2微米。同时,由于测量过程中刀具高速旋转,测量状态与实际加工状态几乎一致,提高了刀具的实际精度。由于采用了激光技术,该工具可以扫描刀具的形状和测量刀具的轮廓,并可以监测多刀刀具的单刀片损伤。其主要缺点是结构复杂,需要额外的优质气源来保护内部结构,成本高,主要适用于高速加工中心。
机内对刀仪的一般功能及优点
(1)刀具长度/直径自动测量及参数更新:刀具旋转时进行长度/直径的动态测量。测量参数包括机床主轴的端跑偏/径向跑偏误差,从而得到机床在高速加工时的“动态”偏置值。同时,工具参数的自动测量,可以在任何时候进行,从而极大地消除机床的热变化工具的“改变”参数引起的形状和测量结果自动更新参数表的相应工具完全避免造成的潜在风险的手工工具设置和参数输入。
(2)自动监测刀具磨损/破损:在实际生产过程中,当工具磨损或破损(破碎),运营商很难及时发现并纠正它(特别是钻直径较小的工具),导致更多的后续工具损失甚至工件报废。使用机床内的刀具对准仪,刀具加工完成后,再放回刀具库一次,即可自动测量刀具长度。在正常磨损情况下,磨损值可自动更新为刀具损坏参数。如果磨损过度,则可视为刀具损坏(断裂),因此操作者可选择更换新刀具进行下一个工件加工或自动停机报警,提示操作者进行刀具更换。从而提高了产品质量,降低了刀具损失率或报废率。
(3)机床热变形自动补偿:机床在生产加工过程中,随着环境温度的变化和工作负荷的变化,随时都会发生机床热变形,进而带动机床发生变化。结果表明,同一机床在车间加工的产品,其尺寸精度在不同时间段有较大的波动。在机床上使用刀具整定仪后,刀具参数可在加工前或加工过程中随时自动测量和更新。每一次测量都是对机床当前热变形下的刀具进行设置,从而大大降低了机床热变形所引起的误差。
(4)刀具轮廓测量与监控:在成型刀具等特殊加工中,利用机床外的对刀仪测量刀具轮廓,判断刀具状态是一项耗时、复杂的工作。同时,对操作者的刀具对准技术要求也很高。此时,如果使用机内激光对刀器,激光束可以随时扫描、测量或监控刀具轮廓,并根据需要自动更新相应的参数。
|