没有应用对刀仪的机械加工过程中,工件装卸、刀具调整等铺助时间在加工周期中占相当大的比例,其中刀具的调整既费时费力,又需要试切、测量。每把刀具的偏置值,是对每把刀具进行仔细的试切后,测量、计算、补偿(手工对刀)才可得出,稍不小心还会报废工件。更换刀具后,这项工作还要重新进行。统计资料表明, 加工一个工件,纯机动时间大约占总时间的55%,装夹和对刀等辅助时间占45%。因此,对刀仪便显示出极大的优越性。启用机加工中心对刀仪,能极大程度的减少因人为操作对刀校刀不准确、刀具破裂、折损、磨损未能及时发现所产生的不良品或废品,缩短刀具调整时间,提生产效率实现。
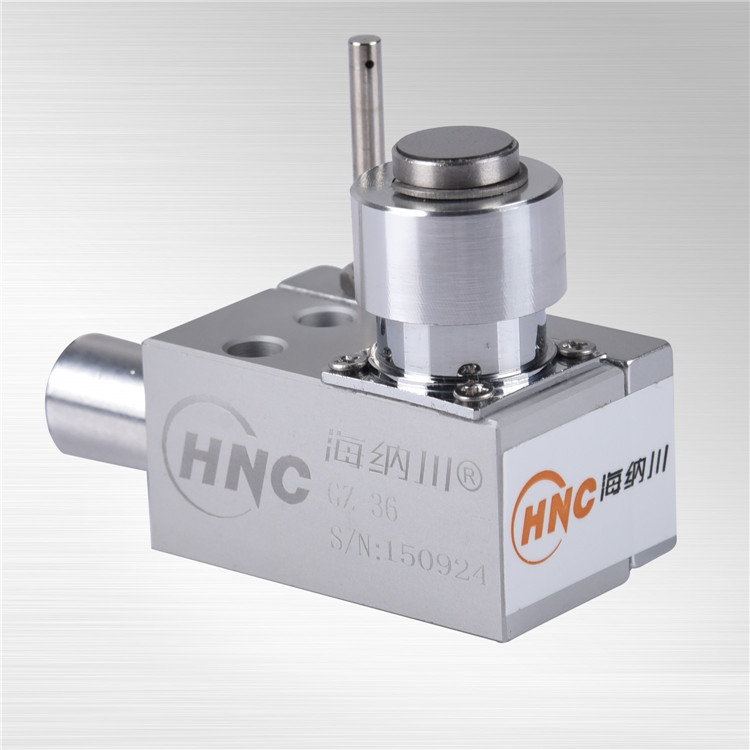
自动对刀仪是利用车床本身的位置测量系统工作的。总的来说,虽然它附属于发动机车床,旨在提高车床加工的效率和精度,但作为一套独立的仪器,普通车床刀具的研究与自动化仪器设计应该包括刀具原理的研究与实现,精密机械零件的研究与实现,电气控制、自动操作方法、刀具仪表误差及精度分析等。机械部分是自动刀具仪表的主要部分,主要包括传感器的设计和连接臂的设计。传感器的设计尤为关键,这就要求传感器能够适应内孔车刀、端面车刀、螺纹车刀、外圆车刀等不同的刀具。另外,传感器的表面应具有硬度要求,不能因为频繁的撞击表面而产生小凹坑,影响刀具仪表的精度,当然也可以对传感器探头进行磨削;传感器应保证所需的精度;传感器结构设计合理,重量不宜过大,安装方便,适合工具的对中和操作。电气控制部分主要包括接口电路的设计。刀具接触传感器后,应在刀具仪表上显示声、光信号,以便操作者及时操作。传感器的触发信号应能准确地反映在数控系统中。为了研究刀具补充算法,根据该算法对系统进行参数化编程,获取刀具尖端信息,并对刀具补充进行分析计算。
试切
1.在实际加工中,通常是各把不同位置的若干把刀具(即各把刀具的刀尖在刀架上相对于某固定点的位置各不相同)加工同一轮廓尺寸的工件,而编程时往往都建立统一的坐标系,要求使所有的刀尖都移到坐标系中的一个基准点上,或者以一把刀为基准设定工件坐标系,因此须将其余刀具的刀尖都偏移到此基准刀尖位置上。利用刀具位置补偿即可完成。
2.对同一把刀具而言,当刀具重磨或更换新刀后,再把它准确地安装到程序所设定的原位置,是非常困难的,总是存在位置误差,这个位置误差在实际加工后即成为加工误差,此时,需通过刀具位置补偿功能来修正刀具安装位置误差。
3.每把刀具在使用过程中都有不同程度的磨损,而磨损后的刀尖位置与编程位置存在差值,同样会造成加工误差,这种误差也可通过刀具位置补偿功能来纠正。
其它对刀方法:
对于装有多把刀具的普通车床而言,每把刀之间也存在着位置偏差,如果逐个去用试切法确定刀补值,势必会造成精度下降,而且效率低下,费时费力。自动对刀仪对刀时先设置标准刀,用试切法对标准刀进行对刀,其它刀具相对于标准刀的刀补值是通过对刀仪的传感器来获取,由数控系统计算而得,这样各把刀相对于工件的刀补值也就确定了。自动对刀仪刀补值的设定与手动对刀法所不同的是它能自动将信息捕捉并运算得到刀补值,将其存储起来。简单地说,自动对刀仪的对刀原理就是通过对刀装置不同刀具相互之间的位置予以确定,由CNC系统计算出位置补偿值(刀补值),并将刀补值储存起来的过程。
一般没有装对刀仪的车床,在加工零件时,通常用来设置用于切割零件的刀具。针尖加工零件时,输入所用刀具的几何尺寸(刀具长度补偿),然后测量加工零件的实际尺寸,修改刀具的几何补偿值和零件的加工工艺,使机床测试时间长,试样浪费增加,效率低,不利于零件的加工实现自动处理。用普通车床操作人员对刀具装置可根据工艺要求进行刀具准备,当加工零件时,当刀具装置收到机床立即停止移动的信号,信号反馈给数控系统,系统自动发送测量值的几何补偿,然后根据相关零件加工程序的测量值修改操作者。分析了普通车床自动对刀仪存在的技术问题,介绍了自动对刀仪的概念,分析了对刀位置偏差产生的原因,介绍了对刀量的确定方法。希望能对提高普通车床加工精度的效率起到更大的作用。
BV认证:关于数控车床对刀仪使用的传感器最常见的类型是X,Y方向两根光栅尺,通过数据线,接口,处理模块,将光栅尺的光电信号转换成坐标显示屏的数据读数。图像处理部分是最简单的,现在最常见的就是放大直读型,把道具的投影放大几十倍然后投射到一个刻度屏上,刀尖对准刻度中心之后,读取显示器上的坐标读数即可。这种结构简单,造价低廉,使用可靠。
|