数控加工中心对刀仪的设计
机床为达到用户生产设备的精度和效率而安装的各种精密设备,机床用自动安装的模板,刀具的相对位置,并根据btais刀具的自动测量结果,零件加工设备精度更高。
近年来,随着科学技术的发展,机械产品变得越来越复杂和复杂,要求机床能够适应产品的变化。其次,简单的数控机床上必须安装多个刀具,由于刀具类型不同,各点的位置和长度不均匀。必须测量每个刀具并计算刀具的附加值,以便程序可以继续操作并生产合格零件。另一方面,刀具的手动操作比较复杂,误差较大,对于需要频繁更换刀具的小批量生产的零件,增加了刀具的工作时间,降低了加工效率,阻碍了加工的自动化,也使加工的优势发挥出来中心操作困难。如果使用自动刀调整装置,则在取下标准刀后,自动校正其他刀与标准刀位置的偏差,使每把刀的刀补既精确又实用。对于产品更新换代频繁、生产周期短的产品的处理是非常有利的。
点攻击机由数控机床制成,使用机械触发传感器,通过控制刀具移动路径触发传感器。刀具附件简单,易于维护,提高了生产率,降低了加工成本。
数控铣床加工中心介绍
数控加工中心是将机械设备和数控系统结合起来加工相对复杂零件的高性能自动化机床。数控机床中心是目前世界上生产量最大、应用最广泛的数控机床之一。其综合加工能力高:单负荷可进行较多的加工操作,加工精度高,适合加工中等难度的大批量零件;效率比常规设备提高5-10倍,因为它允许执行许多常规设备无法执行的加工过程。因此,它更适合于更复杂的形状和要求很高的精度,工作在一块或生产中小型系列。立式加工中心具有直线插补、圆弧插补、快速定位、坐标系调整、刀具偏转、电源维护、循环启动、循环设定、自诊断、误差补偿和程序存储等功能。机床具有良好的动态性能、运动精度的精确控制、稳定恒定的加工精度,能进行钻、钻、拔、磨、铣表面、沟槽和表面。
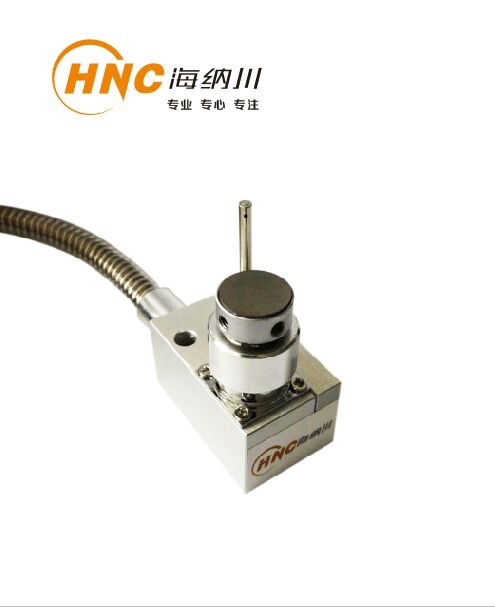
对刀仪的结构及原理
刀具的作用是建立工件坐标系,也就是简单地确定工件在加工中心工作台上的位置,这实际上就像找到工件坐标一样。表坐标系中的切割点。加工中心在选择刀具之前,垂直于刀具,刀尖刀具刀具项目相对于刀具上的起始件的移动都基于参考件的点(在零件或位置期间已经完成),也可以在装配或工作站的某个时刻,前提是该点必须与零件定位的参考精度同时进行。
加工过程中刀具磨损或破损的自动控制、报警和补偿。未配备刀具的机床上的磨损值补偿是一项费力的工作,它需要多次停止以手动测量零件尺寸并手动修改获得的磨损值。安装部分攻击机更方便,特别是HPPA或HPMA机。首先,根据刀具的磨损规律,在干燥一定数量的零件后停止机器并使用调整刀具再次调整刀具就足够了;而后者在程序中设置要执行的加工循环数,然后执行刀具的单个自动调整就足够了以便进行修理工作。
基于直线工件自动调整的原理,这种人机调整提供了最小的测量力而无需横向扭曲。即使是最灵敏、最简单的工具和最小的直径,也能实现非常精确的测量。微格栅的内部使用:(1)无机械磨损;(2)长期使用时保持极高的精度;(3)其他产品第二,使用一段时间后精度降低。对于刀具断裂报警或刀具磨损一定后,根据刀具的允许磨损量设定“极限值”。
对刀仪的作用
通过测量和补偿刀具在正负X、正负Y和正负Z六个方向上的偏转,可以有效地解决由于手动操作刀具而产生的误差和效率低下的问题。无论使用何种刀具,在铣削轮廓时,必须调整或补偿涉及铣削的刀具的所有点或轴,以便完全位于房间坐标系的同一理论点或轴上。对于动态旋转刀具,除了测量和补偿沿刀具长度的偏移量外,还必须测量和补偿刀具直径方向的偏移量(刀具以轴为界的两个半径的偏移量)。否则,加工中心无法保证更高的精度。如果使用微调器调整设备,则结果不同,因为自动微调器调整允许您自动设置相对于工件坐标系的微调器偏移值,从而自动建立工件坐标系。在这种情况下,不再需要在加工程序中使用手动输入来建立工件坐标系。
当刀与刀相对时,刀尖必须与刀尖相对。”“切削点”是指刀具位置的参考点;对于端铣刀,切削点是指该点。刀具的作用是确定工作台坐标系中切削点(或工件原点)对中的绝对值,测量切削点偏差值,而切削点修正的精度直接影响加工精度。在实际生产中,单刀难以满足工件的加工要求,一般采用多刀加工。在使用多个刀具的情况下,更换刀具后刀具端点的几何位置会发生偏移,因此,当不同刀具在不同的起点位置开始工作时,必须确保程序正常运行。该项目的主要技术创新是在机床上设计了一种接触式自动调整工具,使刀具在数控加工前进行调整,提高了生产率,降低了加工成本。
对刀仪的使用方法
(1) 高精度电子自动刀的使用率是必要的,以尝试触发(传感器)精密测试头、短时间刀具,利用系统测量装置测量的机床,通过不同的尖端,在坐标点(x,y,z),然后顺“刀垂直用主轴数控加工中心(CNC),进口数控系统面板在M6T1),指令下,把它们放在1个切纸机(z轴)上,而不是用手轮旋转轴为z轴的脉冲缓慢移动,当测量中心为L的刀的“曝光”尖端时,手轮的Z轴脉冲被设置为第一个齿轮;此时,脉冲手轮的Z轴每转动一格下降0.01 mm。
(2) 此时Z轴的相对值固定在0,当刀具的点与点攻击机的板接触时。1号参考刀的刀尖点目前是测量所有刀具的参考点;该点由手表指针清楚地指示和固定。对于其他刀具,按这对刀具的切割板就足够了,因此数值在刻度0上进行,这意味着刀具的点正好在参考刀具1的点的参考点上。
(3) 用手轮快速提升Z轴(脉冲设置为100报告),让手表指针自动返回其位置,然后将1号刀放回刀库,并在加工中心主轴上更换2号刀。慢慢地让主轴下降,使其从点击机的切板上接近,并改变1速飞轮Z轴的冲量;慢慢转动手轮,使2号刀的点移动“刀”上的切板,直到数值等于零,然后,2号刀具点的位置与1号刀具的参考位置0重合。此时,数控系统中显示的Z轴的相对值是刀具2长度补偿值,该值被输入到数字控制系统的刀具2长度补偿参数列表中。其他刀具也用同样的方法进行了调整。
结论
数控加工中心采用自动对刀仪加工,大大缩短了加工机床所需的时间,经济效益可观。而对于带有数控机床的自动切刀装置,则按照刀具加工的规定,在毛坯上,当装置接收到刀具的信号时,停止机床的数控信号系统,在补偿系统中自动测量数值,此时提供数值根据测量的变换值对相关零件进行变换。自动调整刀的使用缩短了试验刀的工作时间,降低了人为因素,大大提高了自动化水平。
|